Optical force feedback
for endoscopic surgery
This is one of my project (last) as an undergraduate student within the BEAMS (Bio- Electro- And Mechanical Systems) at the Université libre of Bruxelles under Pr. Alain Delchambre.
Background
Endoscopic submucosal dissection is a minimally invasive procedure to remove a tumor from the gastrointestinal tract. This special operation uses an electrosurgical knife that applies a high-frequency, high-voltage current to cut the biological tissue at the submucosal level. However, this difficult procedure requires great care not to perforate the muscularis and limit the operation to the mucosal and submucosal region and represents a steep learning curve for practitioners. We could try to provide a force feeback mechanism to monitor in real-time the applied force but the operating conditions, such as the strict dimensional constraints (~2.7mm) or high temperature due to current, do not allow the practical use of traditional force sensors. The current work aims to use fiber Bragg grating (FBG) based strain sensors to take advantage of their sensitivity to strain and temperature. Specifically, the applied strain is reflected by an optical response via a shift in the Bragg wavelength in a nonlinear relationship. This could allow tip force feedback for a closed-loop force control.

Development
In order to find the non-linear relationship between the wavelength shift provided by the FBG interrogator and the resulting applied force, a calibration testbed is required to gather experimental data. However, manual calibration (accross tip positions, orientation, force levels) took 2 to 3 days of experiments. Such design needed fast iterations so I built a data collection and calibration test-bed using high-precision stepper motors to vary the intensity of the applied force and the orientation (loading and unloading).
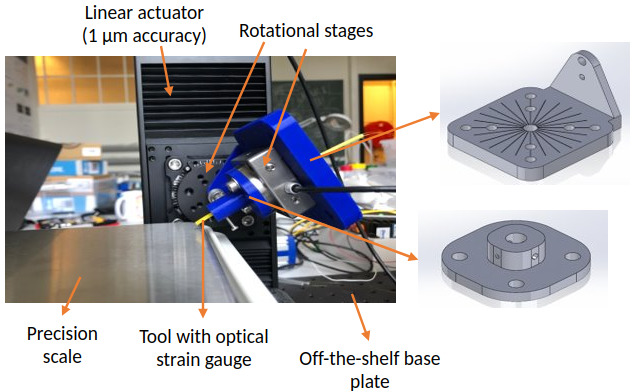
I configured and developed the calibration procedures, the whole motion control system, and synchronous data collection in C/C++. A critical aspect was preserving the integrity of the sensitive tool which required substantial safeguards on the motion control system.
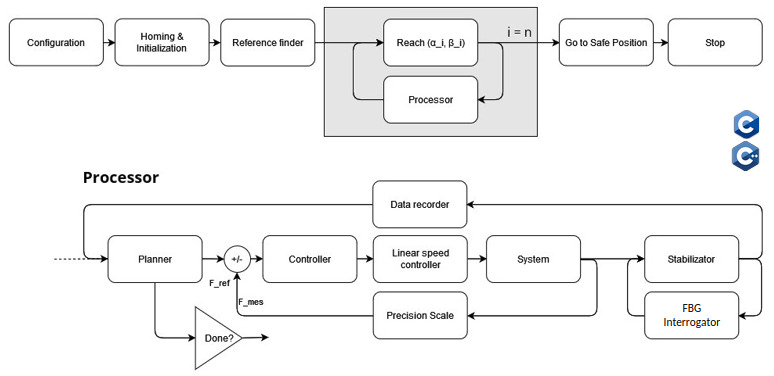
Results
As the table shows, testing and calibrating designs went from 2-3 full days of experiments to a single hour worst case (~30min). The accuracy of measurements improved bu two orders of magnitude. Note that static calibration was now truly enabled since reaching steady-state was impossible manually. I also built an easy-to-use interface using Qt in C++ to configure the hardware and launch and monitor experiments in real-time.
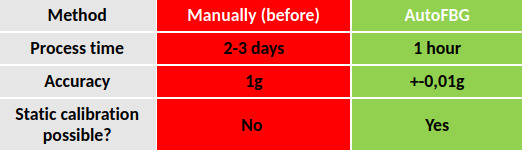
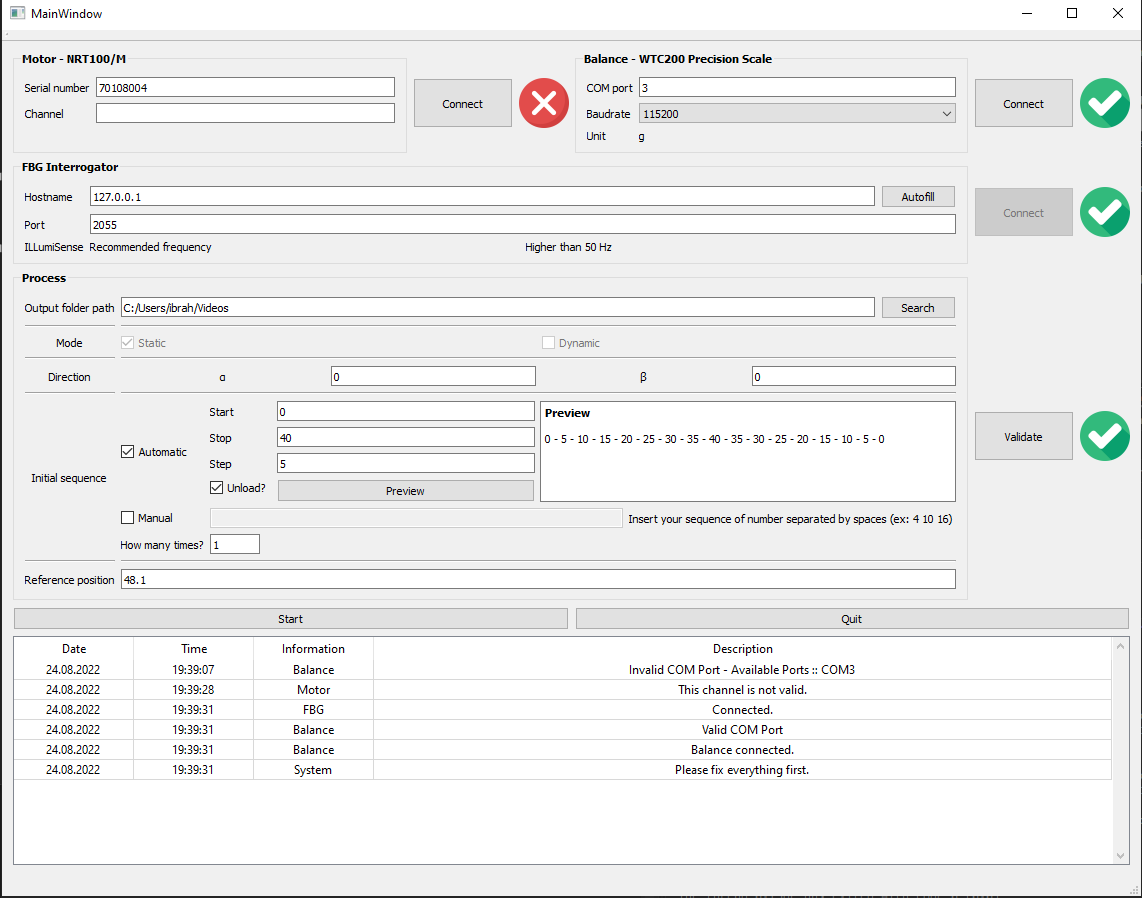
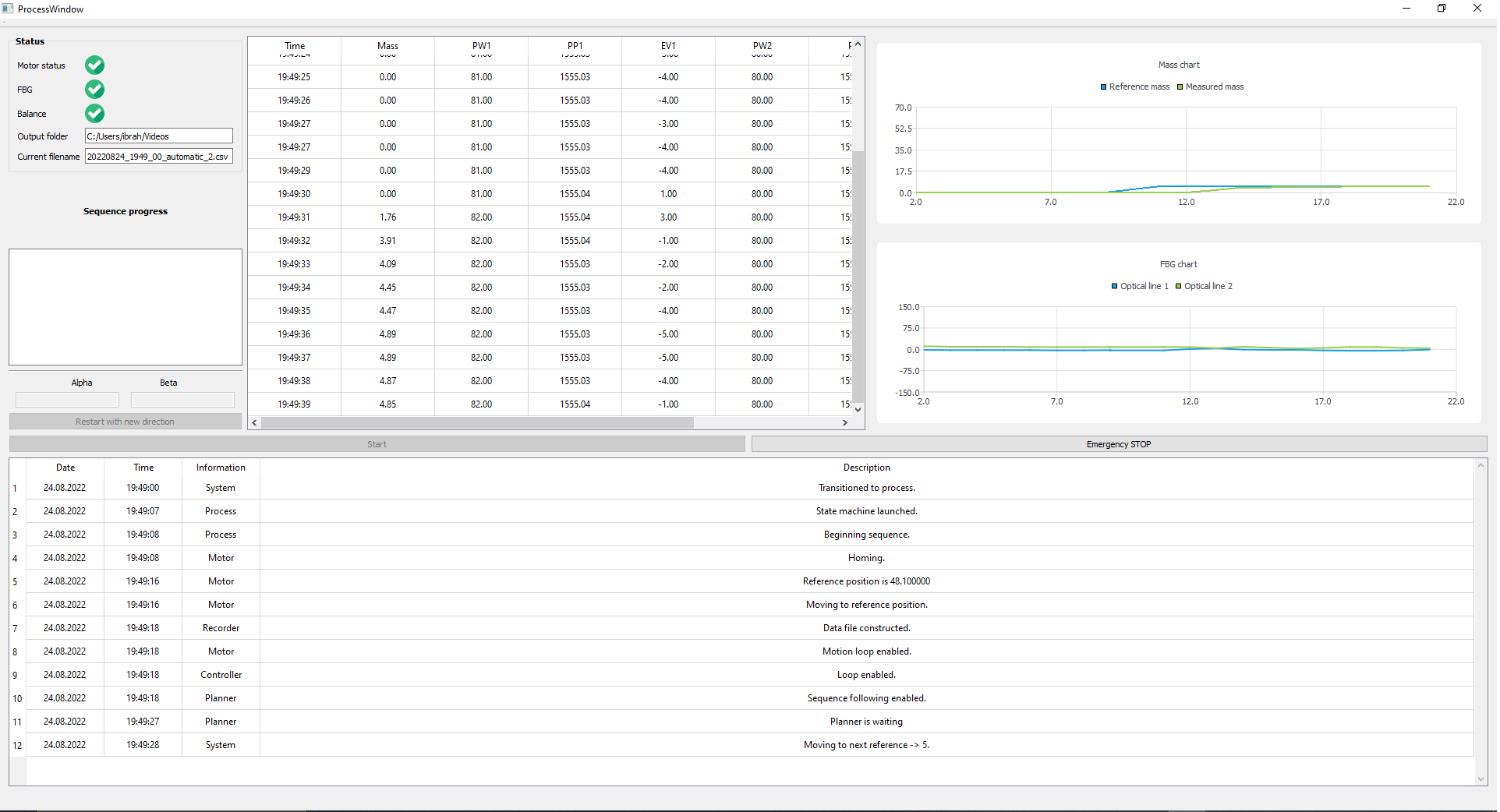